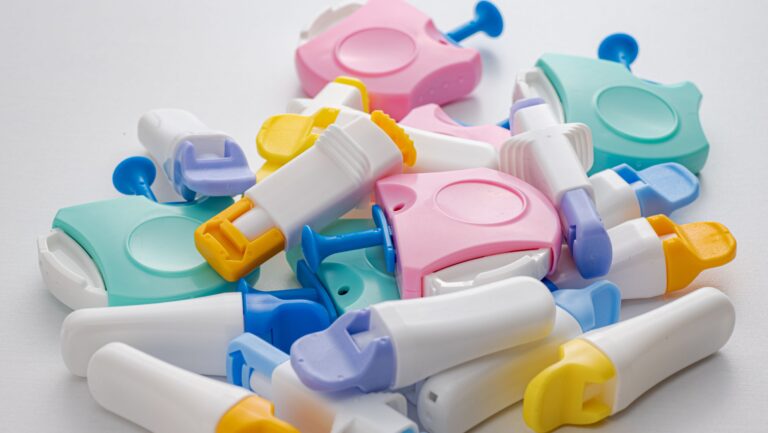
Medical device
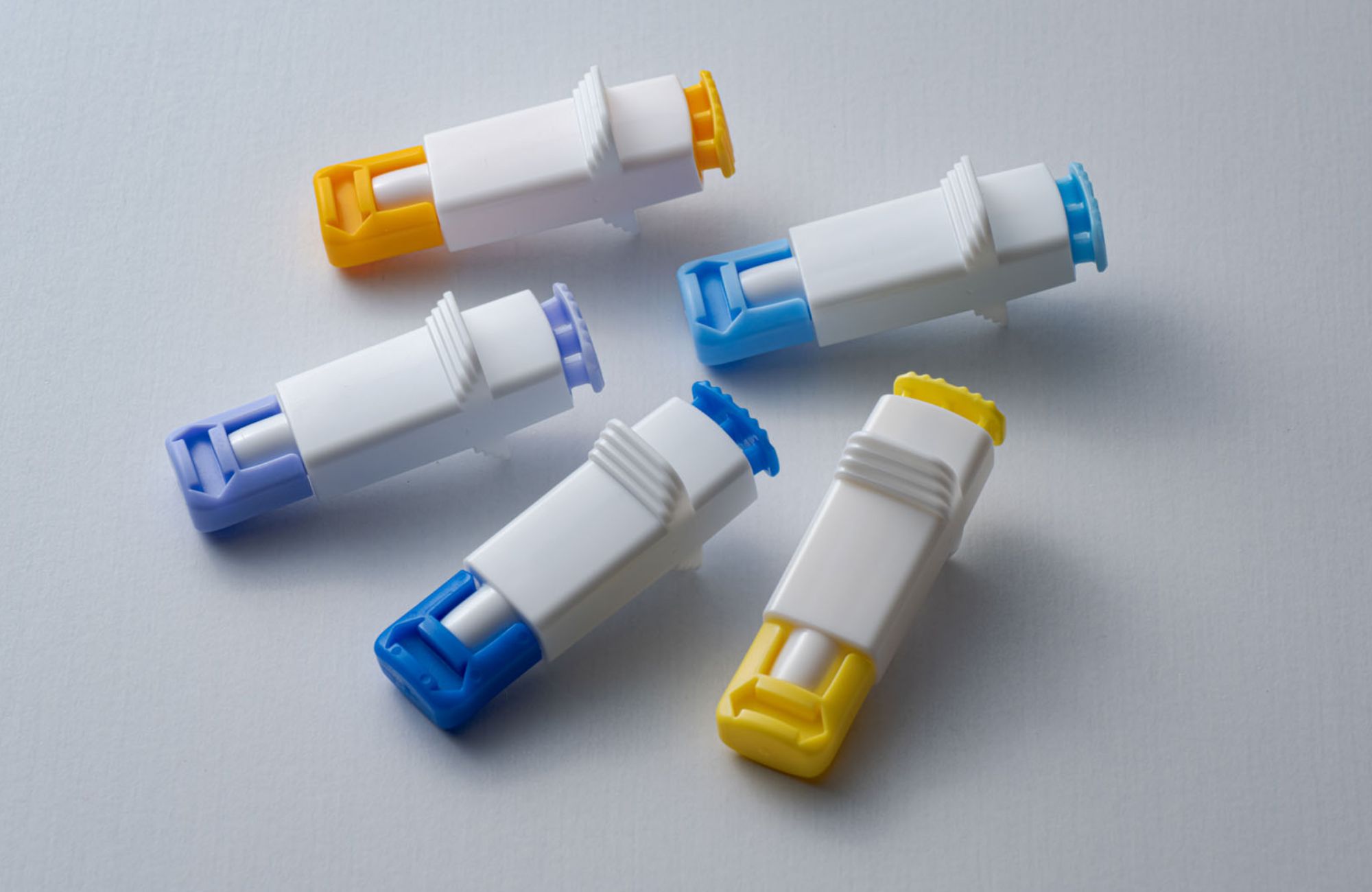
Medical device
Asahi Polyslider's medical business has grown alongside the development of our flagship product, the lancet (small volume blood collection device), which holds a significant share of the Japanese and international markets.
We began full-scale production in the late 1980s and have continued to steadily develop products that meet medical device regulations and quality standards not only in Japan, but also in Europe, the U.S., and other countries. In the 2000s, we began developing our own proprietary products based on the experience we had accumulated, and we have been releasing new products in Japan and abroad since 2008.
In the process, we have acquired the know-how to control quality across development, validation and manufacturing, and to handle the fabrication, maintenance and repair of molds ourselves, thereby ensuring continuous and stable mass production. Asahi Polyslider will continue to grow and develop reliable medical devices that meet the quality standards of all the different countries where we do business.
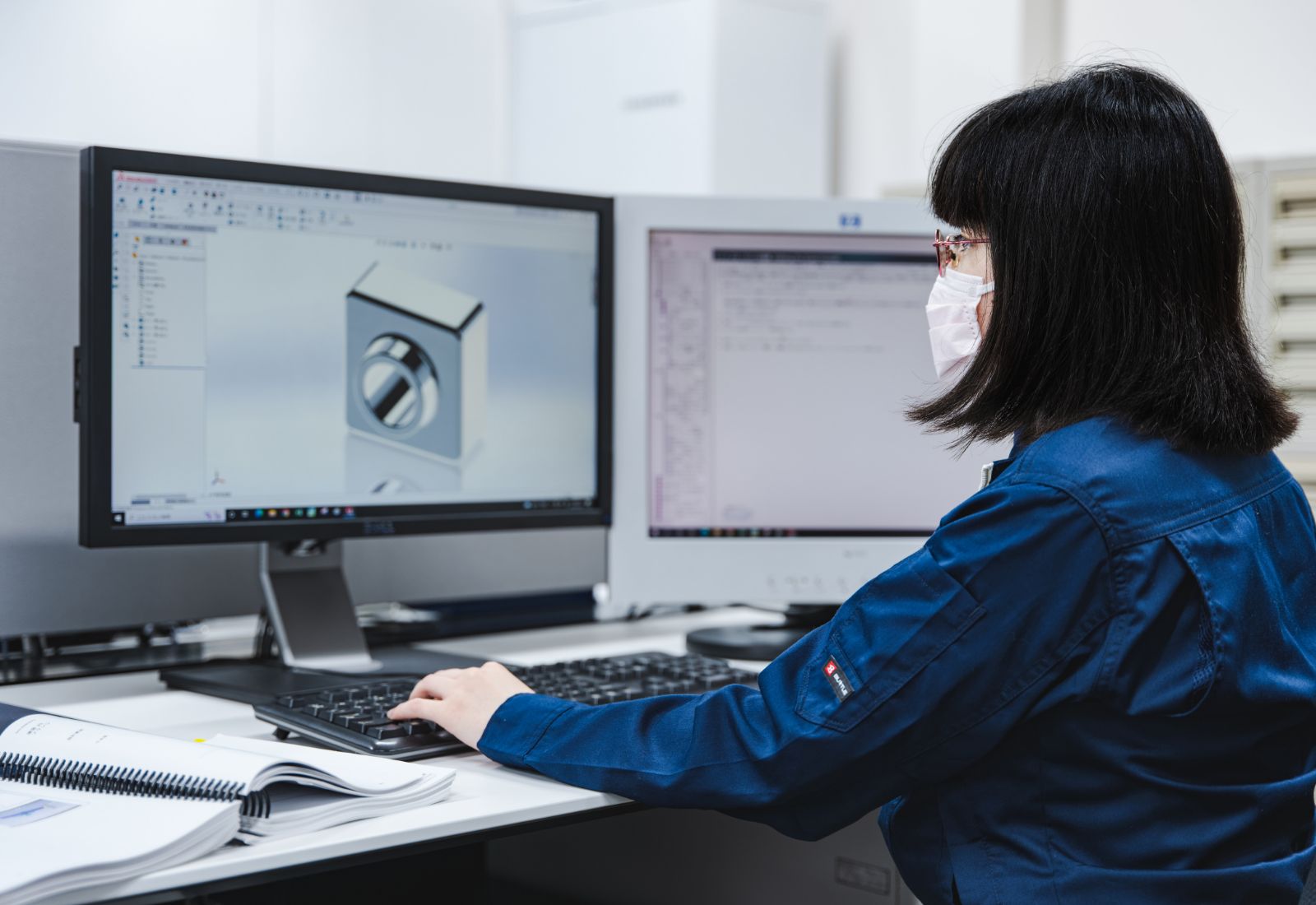
Stress Relief for Diabetics
Lancets have been continuously evolving since they were first used in the medical field. However, using needles daily is still a stressful experience for the patients and Asahi Polyslider aims to offer lancets that cause less pain and therefore less stress. We have been striving to reduce the pain from needle punctures by reducing the needle diameter and minimizing vibrations.
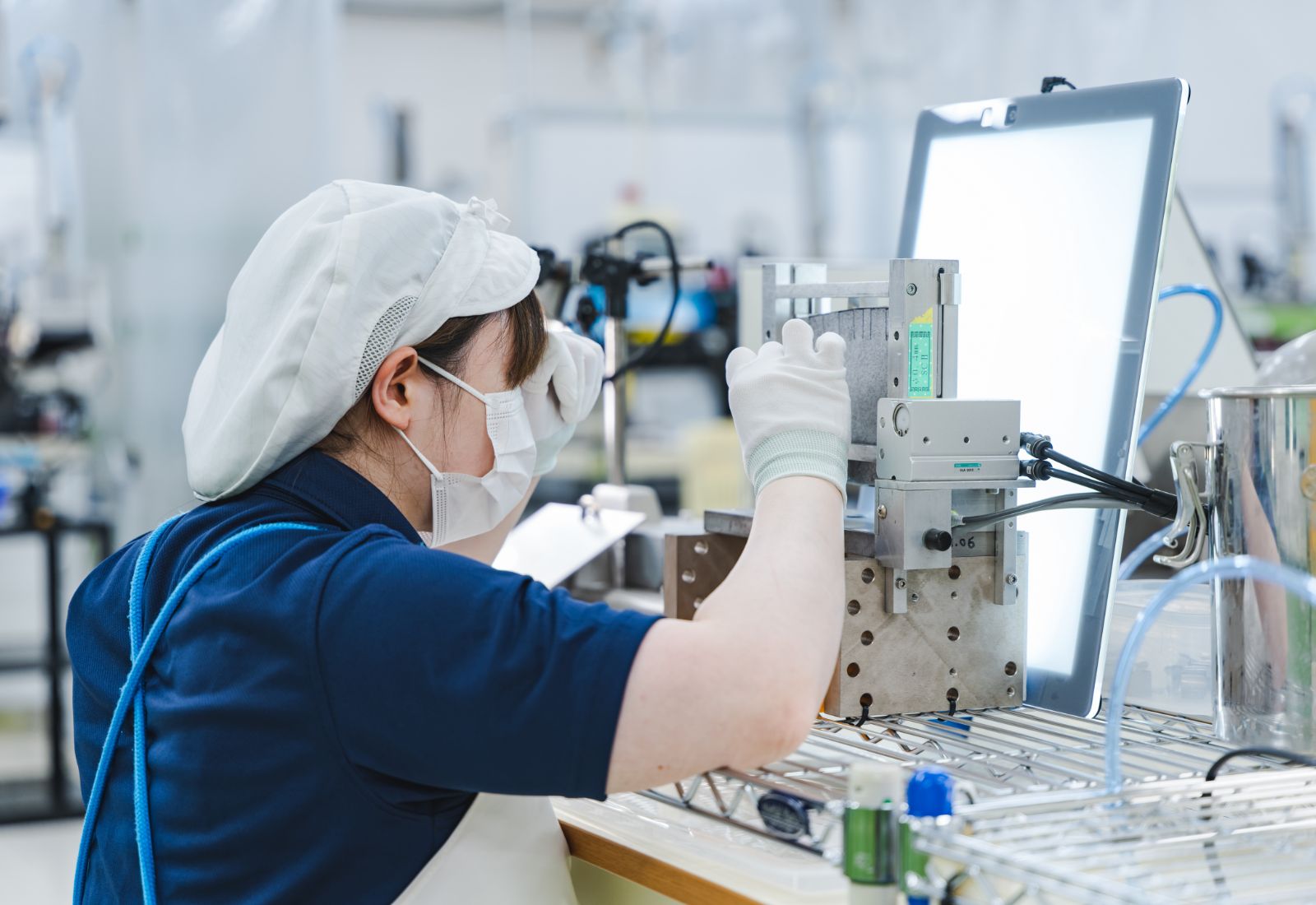
Sought-after Value
The medical world moves forward every day. This is also true of the lancets we supply, where there is a demand for products that are safe, easy to use, and cause less pain. We constantly strive to develop new products. Our engineering team, manufacturing team, and sales team work together as one across all processes, from planning and design to mass production, and the combined and comprehensive strength of our organization enables us to create high-value-added products.
Quality Management System
Under the leadership of top management, the Quality Assurance Department monitors and maintains the entire quality management system.
1 | Identification and review of requirements | Sales Department |
2 | Product design development and review | Engineering Department |
3 | Functional Product Prototyping | |
4 | Design, review, and fabrication of production molds | |
4 | Validation ( IQ, OQ, PQ ) | |
5 | Regulatory submission | Quality Assurance Department |
6 | Materials procurement | Production Control Department |
7 | Needle manufacturing | Needle Manufacturing Department |
8 | Injection molding | Molding Manufacturing Department |
9 | Assembly, counting, packaging | Assembly & Packaging Department |
10 | Inventory management / Logistics | Production Control Department |
11 | Quality Assurance Department | Quality Assurance Department |
Manufacturing process for medical devices
We have achieved consistent, high-quality manufacturing through automation of our manufacturing process. All products that we provide to our customers are subject to strict quality controls across every manufacturing process.
Engineering Department
Design and Development Section
This team designs medical devices and develops new products. Its core tasks are to design products for functionality and manufacturability, create drawings using 3D CAD, and dimensional and performance evaluations of prototypes; all under an ISO 13485 certified design control system.
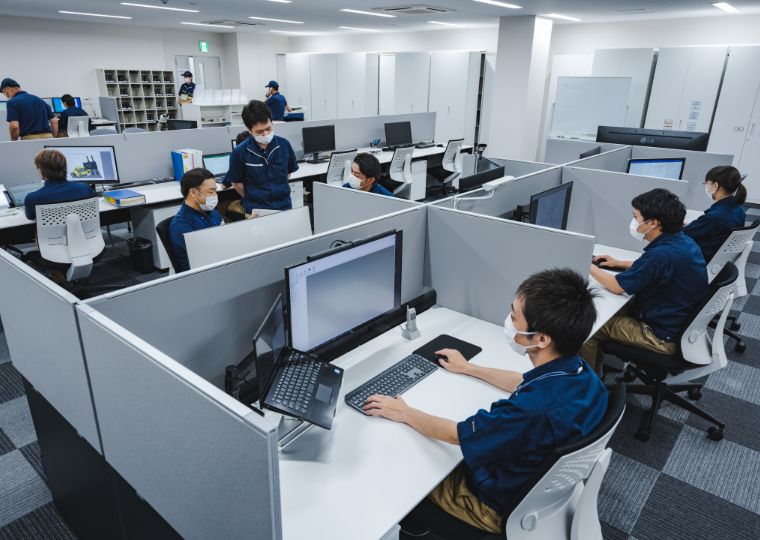

Production Engineering Section
This team works with the manufacturing team to develop and implement efficient and stable production systems. It is made up of employees who have built up the relevant experience at Asahi Polyslider, as well as those who have been recruited from a variety of other fields. The team is also involved in manufacturing process validation for medical devices.
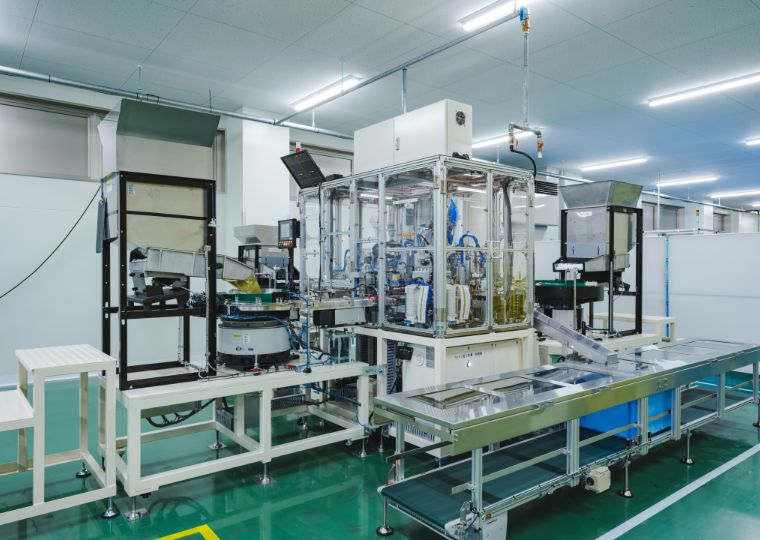
Quality Assurance Department
This team ensures that quality is integrated into our design and manufacturing processes from the beginning of every project to assure stable product quality, providing customers with safe and reliable products. We have built a quality management systems that complies with the necessary standards for medical devices, and is regularly audited for regulatory compliance for many different countries and companies.
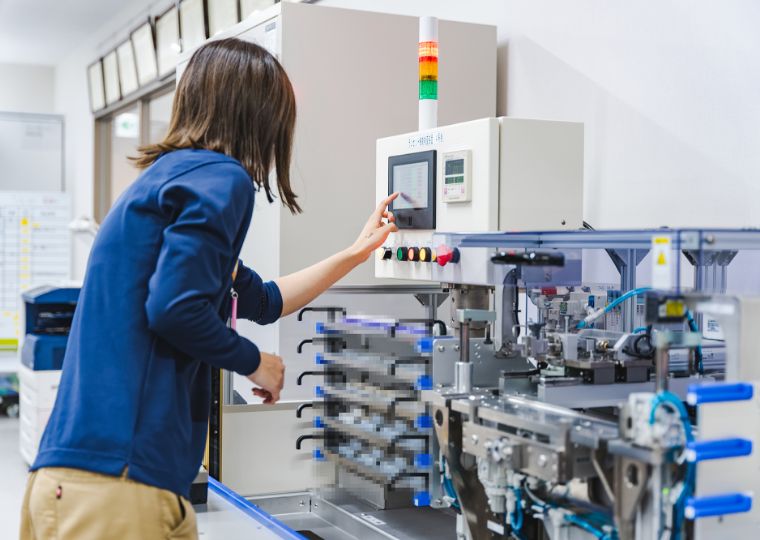
Needle Manufacturing Department
This division manufactures lancet needles, the core of one of our main products. We have automated the various processes, such stainless steel wire cutting, multi-facet tip grinding, and needle tip coating. We have the capacity to manufacture more than 300 million needles per month.
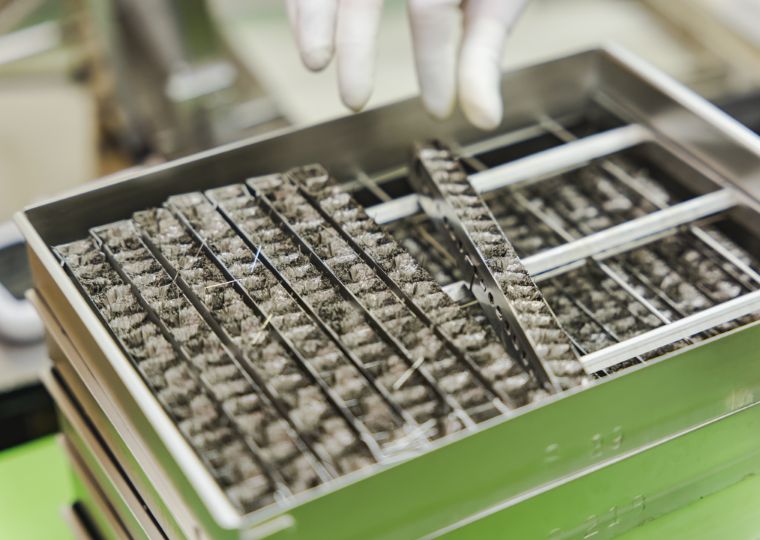
We recognize that medical devices are important products that are directly applied to the human body. While promoting the automation of manufacturing processes, we make sure to carefully inspect our products.
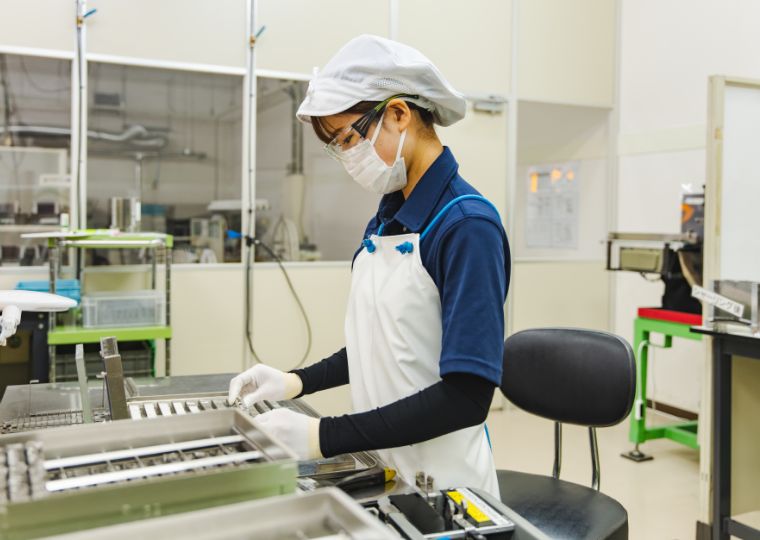
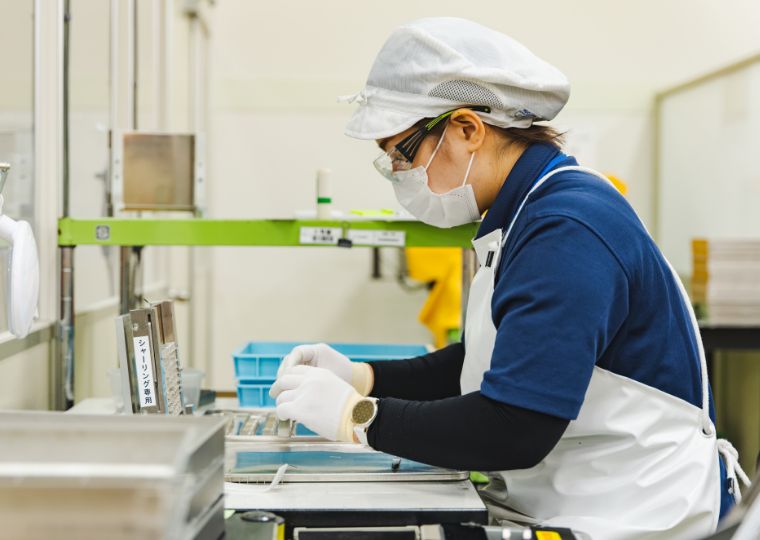
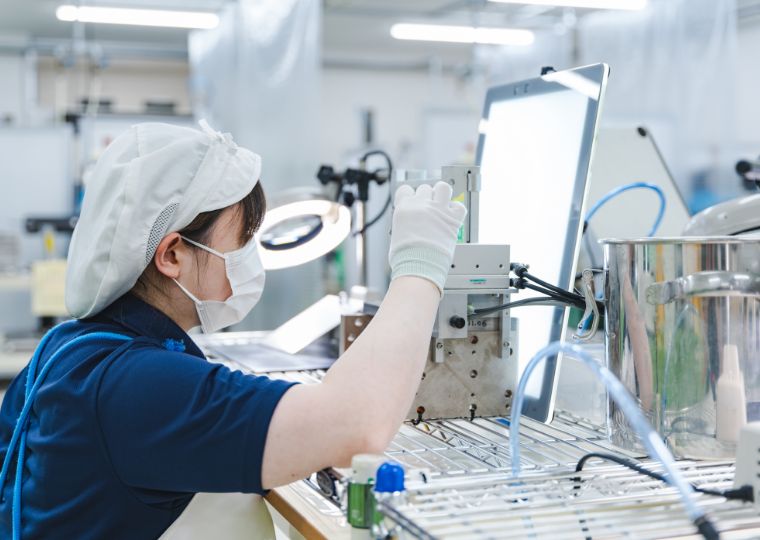
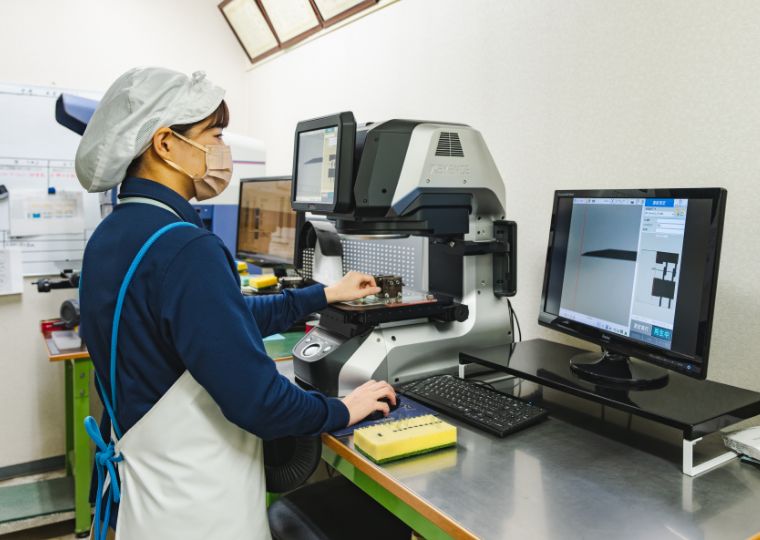
Molding Manufacturing Department
This is the medical device injection molding manufacturing process. Our production facilities have the capacity to fully meet the demands of customers, both in Japan and overseas.
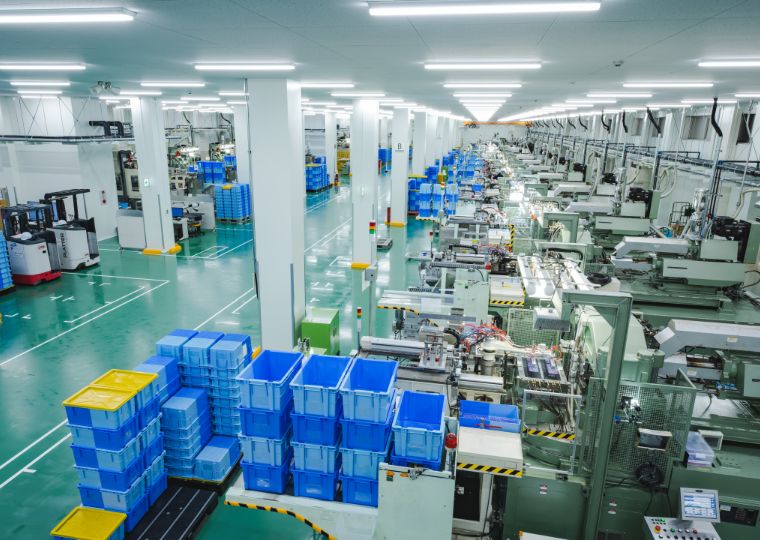
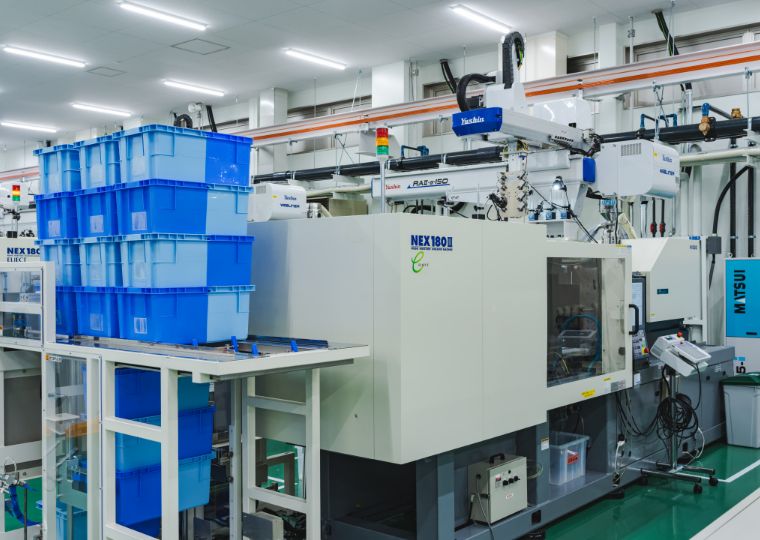
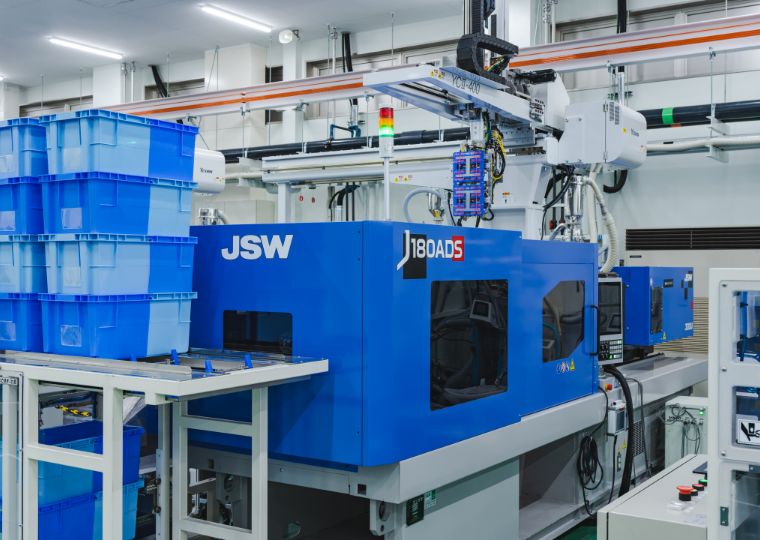
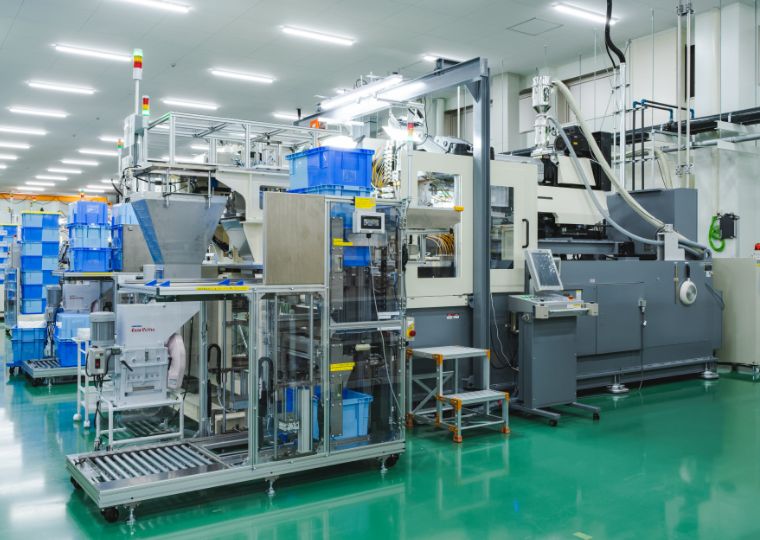
In addition to prototype equipment in the Technology Department, there is prototype molding equipment at our manufacturing room, so that we can perform manufacturing tests in an environment with good reproducibility before starting mass production.
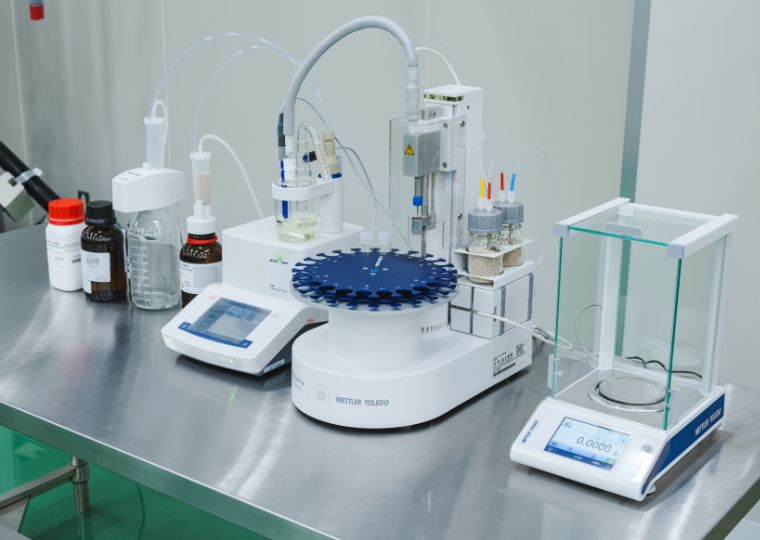
Karl Fischer Moisture Analyzer
This device allows the precise measurement of the moisture content in resins. It can obtain accurate and precise measurements in minutes. An operator can perform the automated moisture content measurement of several samples at the touch of a button. This system is also used to verify the drying, storage, and control methods for humidity-sensitive products and materials.
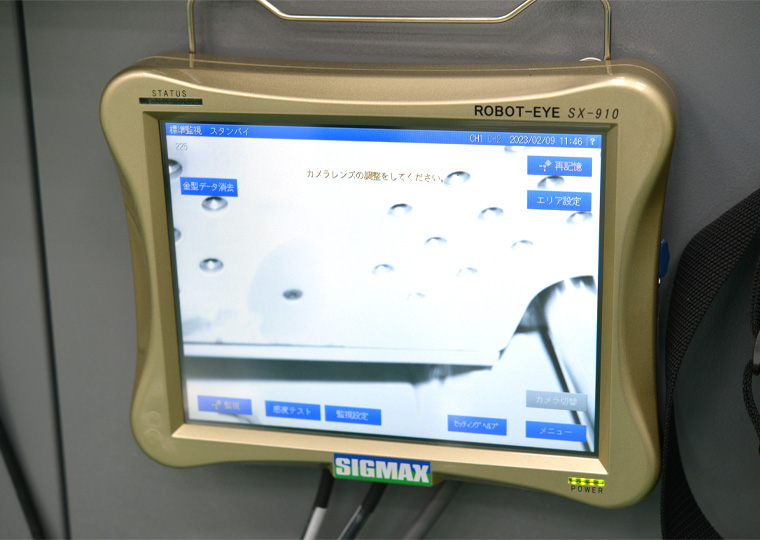
Image Inspection Equipment and Various Sensors
We have introduced image inspection equipment and sensors in various molding and assembly machines and automated machines, enabling us to monitor the quality of product appearances, dimensions, and insert conditions, as well as to protect equipment such as molds, collect process data, and conduct analysis.
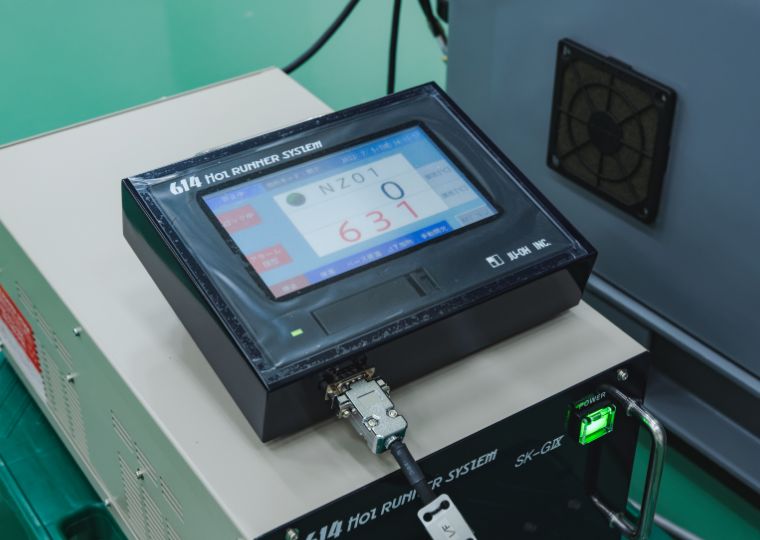
Hot Runner System
We use hot runner systems from various manufacturers, including valved systems, mini-runner systems, and electromagnetic induction heating systems, and can also handle sprue-less, runner-less, and other verification prototypes.
*For example, we have experience with various resins such as general purpose resins, engineering plastics, super engineering plastics, and biodegradable resins.
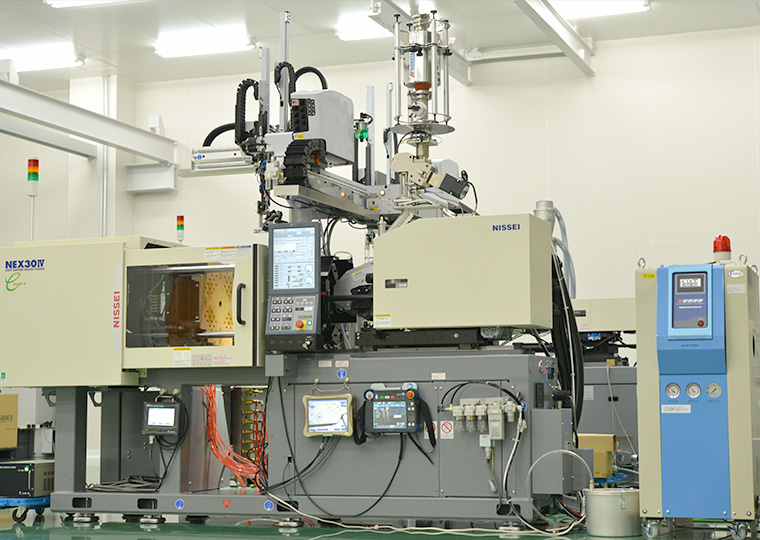
Injection Molding Machine for Prototyping
We have small injection molding machines, both vertical and horizontal, exclusively for trial production. We select the most suitable molding machine model and specifications taking into account various considerations. We have also introduced a number of molding machines that can be customized for mass production according to any unique product requirements.
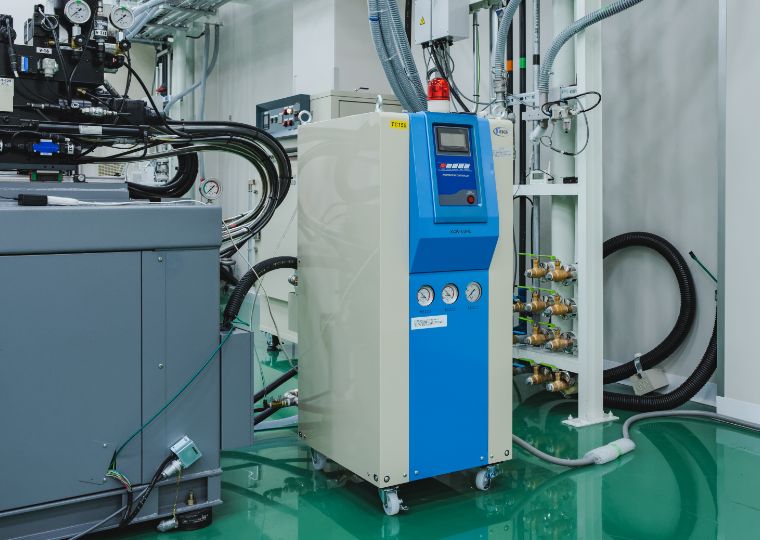
Mold Temperature Control Equipment
Our mold temperature control systems are capable of supplying a large flow of coolant with precision temperature control to the mold under any conditions. The system can handle temperatures from low to high, and supports high-cycle and high-precision molding.
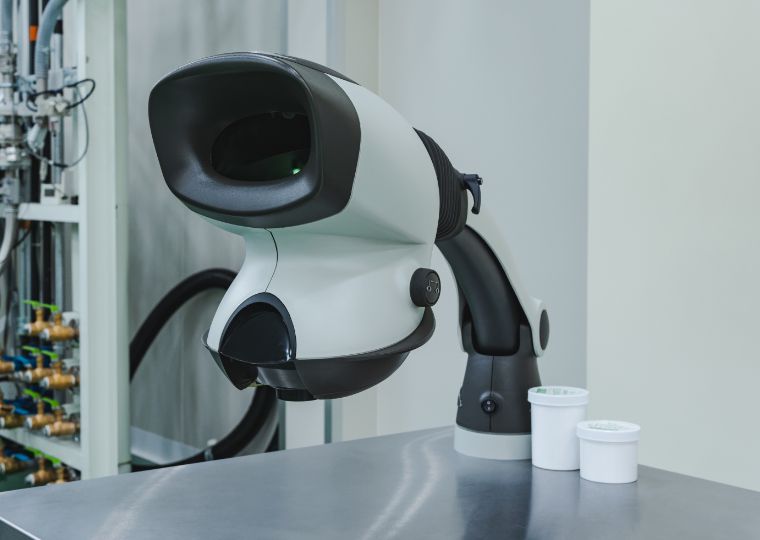
Eyepiece-less Stereo Microscopes
These are eyepiece-less stereo microscopes used to check and inspect the appearance of products during prototyping
We have installed numerous cameras and sensors that enable us to monitor the operating status of all molding machines in real time with automatic monitoring software (PQ Manager, NET100, etc.).
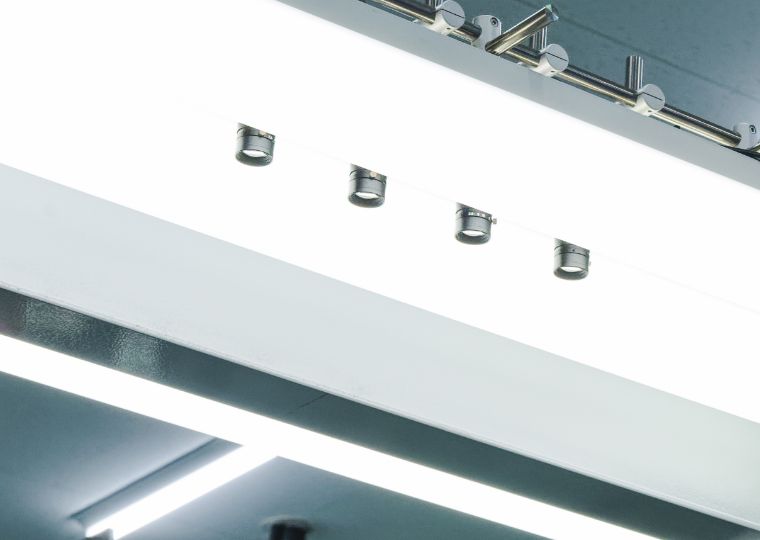
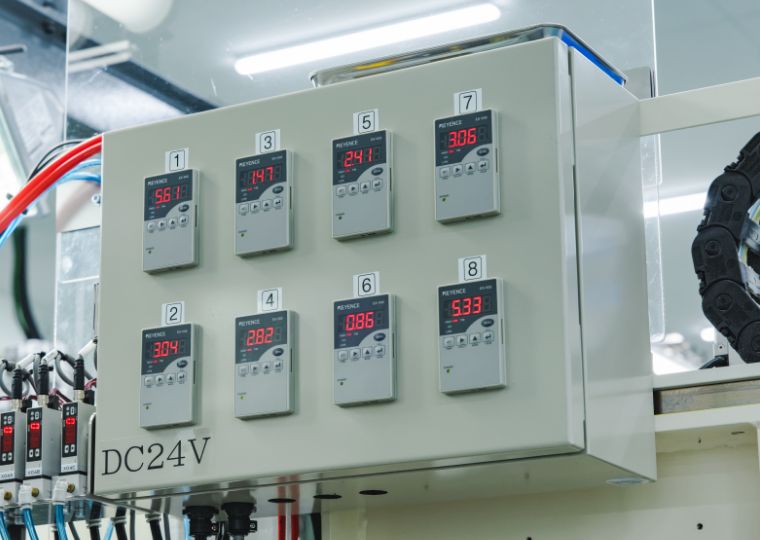
We have automated various processes to make our production lines as efficient as possible. The manufacturing floor has particulate controls and is maintained at a constant temperature throughout the year to create a comfortable working environment that facilitates consistent product quality.
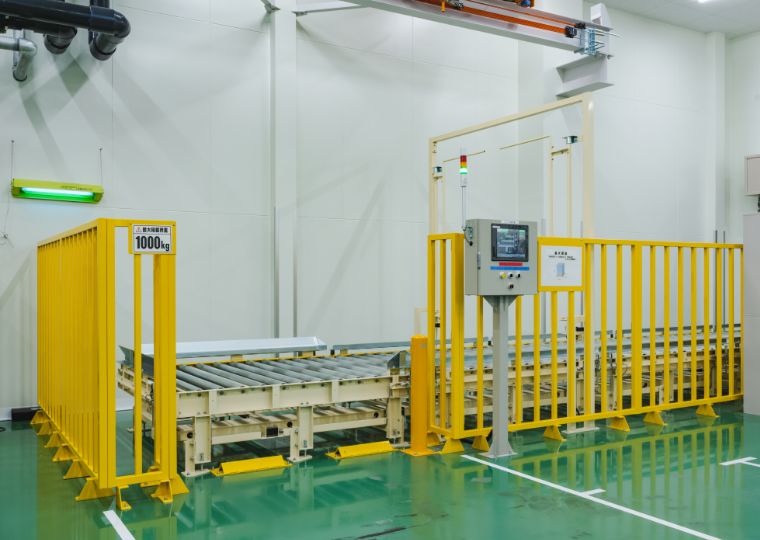
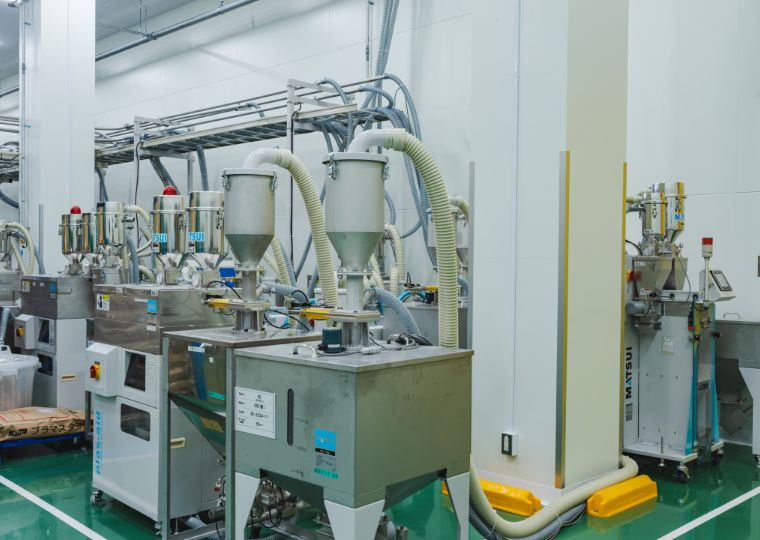
Assembly & Packaging Department
Production Control Department
Asahi Polyslider supplies products worldwide from temperature-controlled, automated warehouses.
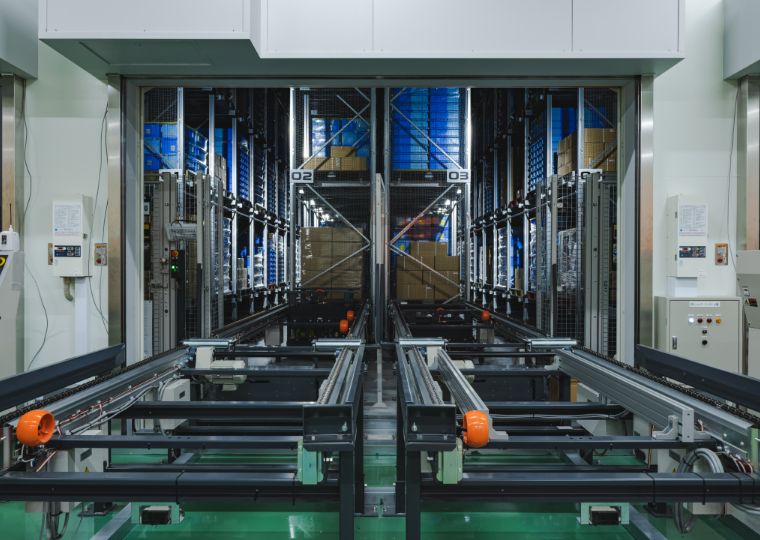
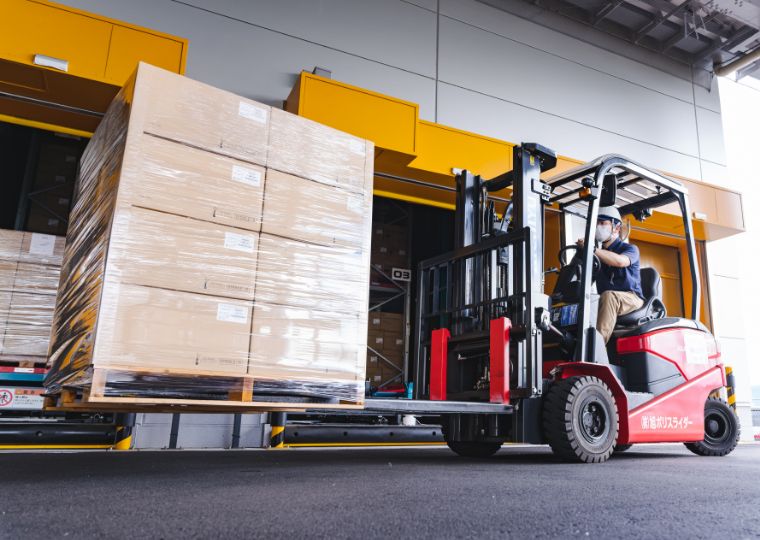
High quality awareness
Asahi Polyslider's medical business has grown alongside the development of our flagship product, the lancet (small volume blood collection device), which holds a significant share of the Japanese and international markets.
We began full-scale production in the late 1980s and have continued to steadily develop products that meet medical device regulations and quality standards not only in Japan, but also in Europe, the U.S., and other countries. In the 2000s, we began developing our own proprietary products based on the experience we had accumulated, and we have been releasing new products in Japan and abroad since 2008.
In the process, we have acquired the know-how to control quality across development, validation and manufacturing, and to handle the fabrication, maintenance and repair of molds ourselves, thereby ensuring continuous and stable mass production. Asahi Polyslider will continue to grow and develop reliable medical devices that meet the quality standards of all the different countries where we do business.
Asahi Polyslider complies with the following regulations, standards, and laws:
Authorization / Registration / Obtained Certifications | |
---|---|
Authorization / Registration | Medical Device Manufacturing Certification |
Second-Class Marketing License for Medical Devices | |
Obtained Certifications | ISO9001 |
ISO14001 | |
ISO13485 | |
MDSAP (Australia, Brazil, Canada, Japan, U.S.A.) | |
Medical Devices Directive93/42/EEC(MDD) | |
*Certification under review | Regulation (EU) 2017/745(MDR) |
Selected Customers
- ARKRAY, Inc.
- Sanwa Kagaku Kenkyusho Co., Ltd.
- Terumo Corporation
- PHC Corporation
- LifeScan Japan
- LifeScan, Inc.
- Roche Diabetes Care GmbH
- Roche DC Japan K.K.